This is how automation works today!
The Modular Transport System combines transport, machining and quality assurance function in a nearly ideal manner. Depending on the requirements profile, the actual transport route can be enhanced by a flexible arrangement of loading robots, measuring and plausibility stations, machining robots, converters or assembly stations. The high level of flexibility is ultimately the result of the overall system reconfigurability and the independently operating functional units.
Product advantages
- Flexible transport system of workpieces, free positioning along the circulation system
- Full-fledged machining axis
- High positioning accuracy ±0.05mm
- Almost any number of shuttles on the circulation system
- Dynamic configuration of groups with flexible control of all - shuttles as master or slave
- Full processing axis can be controlled via NC or CNC
- Synchronous cyclic operation via CAN bus
- Standardized insertion interface for all stations in the cycle
Application scenarios
The Modular Transport System is a modular, flexible, fully scalable transport and handling system with a master/slave and recuperation function.
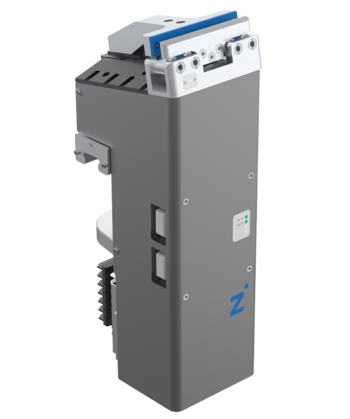
Technology and economic efficiency
Thanks to its modularity, flexibility and scalability, the system can be used either as a transport system or a handling system. The transport modules take care of workpiece transport, while the speed of each individual shuttle or shuttle group can be selected freely. The individually controlled transport units can be used as masters or slaves, depending on the requirements of the MES system. They can operate separately or in tandem. This eliminates fixed coupling of the transport by a continuous conveyor belt, for example.
Viewed over the full life cycle, this new machine concept offers high investment security since the modular design makes it possible to add later extensions through new machining modules. The modules move on a freely configurable track to attain an almost unlimited length and range of variants.
Two impressive innovations
Innovation number one: the high flexibility and broad scalability of the individually controlled transport units, which are controlled as either a master or a slave, depending on the production order. These transport units can carry workpieces of very different sizes, either as individual transport units for smaller workpieces or together in a master-slave assembly for one large workpiece. Innovation number two: An integrated 48 V intermediate circuit buffer. In combination with the recuperation function of the transport units, this buffer reduces load current peaks by approx. 85% and the system’s energy consumption by more than 8%. The production process is interconnected because all processes are directly linked to a higher-level MES system. Thanks to numerous sensors, the current status information can be called up in real time (condition monitoring). Cloud connection is also possible, thereby enabling functionalities such as predictive maintenance and statistical evaluations.
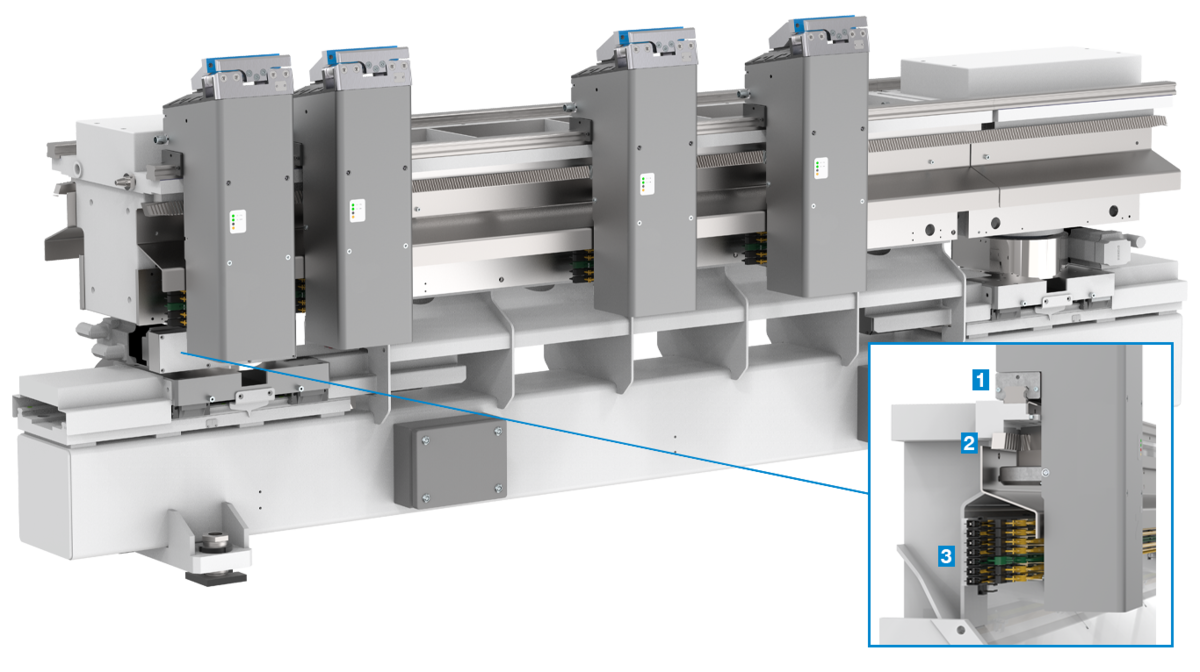
Basic structure of the MTS
- Machine bed made of high-strength aluminum extruded profile, scalable in length
- Central lubrication for rotating movement units
- High-grade linear guides for absorbing weight and machining forces
- Optimized rack-and-pinion drive for the highest requirements on linear drive systems
- Transfer of electrical energy and information via busbars
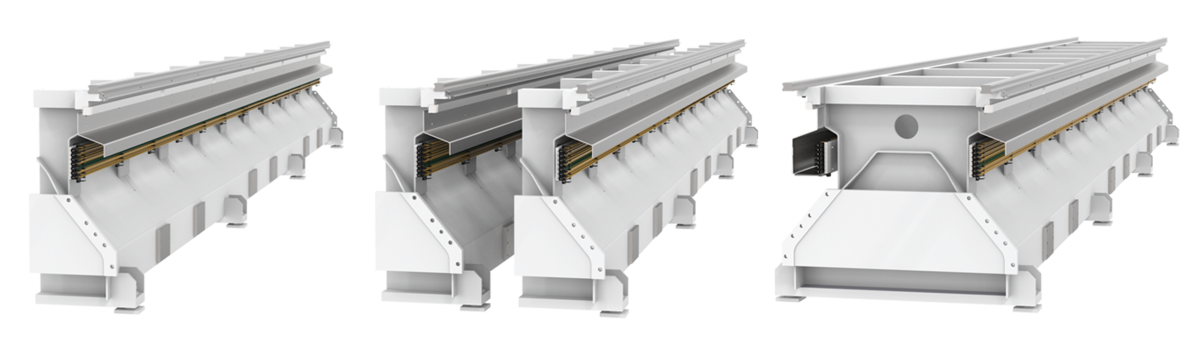
Basic profiles
- Single-track
Reversing operation of the shuttles
Simple design, but continuous material flow not possible - Dual-track
Continuous circulation without changing the orientation of the shuttles
Circulation implemented by means of a linear transfer unit - Double-sided
Continuous circulation with change of the shuttle orientation
Circulation implemented by means of a rotational transfer unit